- The date shall be written in the following formats:
DD/MM/YY For example 25/08/20
Where: DD is denoted to date, MM is denoted to month, YY stands for last two digits of the year
- All documentation of time and verification of time and date stamps shall be performed using a consistent source, i.e. a Slave Clock system where all clocks in production, lab and packaging areas depend on a master clock to assure uniformity of performance.
- Time generated from all equipment and computers used for GxP activities shall be synchronized with the company clock provided in the area.
- Verify the time from the company clock provided in the area where the activity is being performed and not from personal watches.
Time Format
- For all the GMP records change the date after 24 hours cycle daily, i.e. after 23:59:60 or 00:00:00 in the night as per Indian Standard Time.
- Time: Write time numerically in the form of HH:MM or HH:MM:SS, as applicable, in the document using 24 hours cycle daily. e.g.,
For 03:45 AM write 03:45 or 03:45:00
03:45 PM write 15:45 or 15:45:00
12:30 AM write 00:30 or 00:30:00
- Time duration to be written as shown below:
- Note 1) If for some process the observed time duration is 2 minutes and 30 seconds then it should be written as 2min 30 sec and not as 2:30min.
- 2) In case time is printed from a machine or a computer, the time format of the machine or the computer shall be followed.
- Attachments shall be cross-referenced to the parent document and the parent document shall be cross-referenced to the attachments.
- In case of electronic records, all child records of a parent document shall have an indication of the relationship with the parent document.
- Data shall be recorded directly on approved and authorized formats only (e.g., batch production records, batch packaging records, laboratory notebooks, raw data sheets).
- Data for GxP documentation shall not be recorded on unauthorized documents.
- All GxP documents shall identify the significant steps that require checks by a second person while performing the activity (e.g. witnessing dispensing materials for batch production).
- Impermanent records like data printed on thermal paper, thin layer Chromatography (TLC) etc., shall be copied onto a permanent medium and the copies shall be attached to or stored along with, the original signed records.
Handwritten Documents- Good Documentation Practices:
- Use only indelible ink (preferably only black or blue colors) in GxP documents.
- The ink used shall be such that it can be photocopied.
- Write all GMP records only with a permanent BLACK indelible ink pen.
- Use permanent BLUE indelible ink pen for the signing of master documents for all departments.
- QA/QC supervisor shall used BLUE indelible ink pen for checking and approval only.
- The QA supervisor shall use the permanent BLUE indelible ink pen to sign all GMP records, checking or approving the data.
- All entries should concise, legible, unambiguous and accurate.
- Sign on Handwritten records or initialed and dated at the time the information is entered.
- All entries related to experiments being performed shall be done in chronological order.
- In the case of continuous pages of a notebook that are not being used to record data, continuity shall be denoted by recording the reference of the notebook number or page numbers at appropriate places.
- For example, if an experiment is recorded in a laboratory notebook on Page 25 and calculations are recorded on Page 35, a cross-reference linking the experiment with the calculations shall be recorded on both pages.
The following practices are strictly prohibited under Good Documentation Practices:
- Use of ditto marks (“) or down arrows ( ) to fill in repetitive entries.
- Use of pencil or any removable/water-soluble ink.
- Eraser or ink remover use.
- Use of “white-out or correction fluid” to cover recording then write over it.
- Use of a stamp to replace manual dating, initials or signature on GMP documents, except in the case of validated electronic signature.
- When one option is to be selected from several text options, the correct option shall be preferably marked with “√”. (Good Documentation Practices)
- An example is shown below:
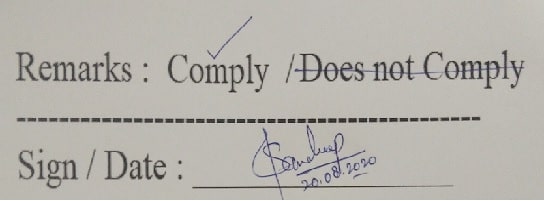
- Working with Blank or Unused page/space:
- Do not leave blank space in any GMP record.
- Blank spaces or pages shall have a single line through them with a signature and date and the reason for the page is blank (e.g. “Not Applicable”, “NA” or “N/A”).
- An example is shown below:
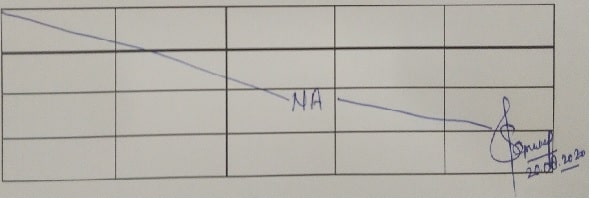
Signature Practices under Good Documentation Practices:
- Use the log for traceability of signatures for GxP records as per SOP Recording of Specimen Signatures of Employees.
- Signatures for all GxP activities shall always be accompanied by the relevant date wherever a separate date column has not been provided.
- Signatures indicate that the Signatory is responsible for the accuracy of data and information for the activity being signed for.
- The Signatory shall confirm the accuracy and completeness of information and data before signing.
- Persons preparing, reviewing, or approving documents or persons recording, verifying, or approving records shall sign and write the current date in the documents.
Note: Current date refers to the date when the document/record is signed.
- All document signatories shall be adequately trained for the activity performed by them.
- For each activity/document (as applicable), each person shall sign (with current date) either as a Doer or a Verifier (also called “Checker”) or a Reviewer or an Approver.
- One person shall not sign for multiple roles for the same activity or entry (e.g. a doer cannot be the “Verifier”/ “Reviewer”/”Approver” for the same activity or entry recorded).
- No employee is authorized to sign for an activity performed by another employee.
- A clear meaning of each signature shall be provided (e.g. “Performed By”/”Verified By”/”Reviewed By”/”Approved By”).
Definitions/Significance of Signatures:
- Prepared By / Performed By / Written By / Analyzed By (also called “Doer”): The signature of the person actually carrying out the operation, test, inspection, calculation, or other actions.
- Entries in the documents/records along with Signature and Date shall be made at the time when the activity is performed (contemporaneously).
- The signature of the “Doer” denotes that the “Doer” has performed the activity and confirms the authenticity of the data as that of the activity performed.
- The Doer shall also check the result for its compliance against the specified limits/acceptance criteria and is expected to inform the respective Supervisor/Team Lead/Manager in case the results do not comply.
- Verified By/Checked By: The signature of the person responsible for witnessing or conducting an independent check to ensure the operation, test, inspection, calculation or other actions followed required instructions and procedures and verifies the entries made by the Doer.
- The “Verifier”/”Checker” shall record and sign concurrently for the ongoing activity being checked.
- The signature of the “Verifier” denotes that the Verifier has confirmed that the entries are made correctly and are complying with predefined specifications/acceptance criteria.
Reviewed By:
- The signature of the person responsible for examining the documentation and certifying that the document/record was prepared/filled appropriately and in compliance with requirements.
- The “Reviewer” shall review and sign (with date) for the activity/document/record being reviewed; the reviewer may or may not be present when the activity is being performed.
- The “Reviewer” shall review the completeness of the document/record and conformance of results recorded during the activity to established process parameters, limits, and other applicable standards that define requirements of the activity being performed.
- The signature of the “Reviewer” denotes that the document/record has been examined, all requirements have been fulfilled and the document/record demonstrates that the process was followed in accordance with the instructions provided.
Approved By:
- The signature of the person accepting the document/record for conformity to requirements.
- The “Approver” shall review and sign (with date) for the activity/documents/record being approved; the Approver may or may not be present when the activity is being performed.
- Review the conformance of results recorded during the activity to established process parameters, limits, and other applicable standards that define requirements of the activity being performed.
- The Signature of the “Approver” denotes that the document/record demonstrates that the process was followed in accordance with the instructions provided and is approved for conformity with requirements.
Authorized By:
- The signature of the person responsible for providing official permission or approval to another individual to perform a particular task.
Designee:
- Reviewers/Approvers may delegate authority to another suitably qualified person to review/approve records, as applicable.
- The designee shall be qualified to perform the delegated task based upon relative job position, training, experience, and subject matter expertise.
- Though a designee may perform the delegated task (of reviewing/approving, as applicable), final accountability of the activity performed by the designee shall reside with the person delegating the task.
- Supervisors of a signatory and/or members of the same department at an equivalent or higher titles may function as designees without prior delegation of authority.
The following signature practices are strictly prohibited:
- Pre-dating or post-dating (backdating) either documents or corrections.
- Pre-dating is completing an activity and then signing/dating that the activity was performed at a later time/date.
- Back-Dating is completing an activity and then signing/dating that the activity was performed at an earlier time/date.
- Signing someone else’s name unless the signer is a Designee and it is clearly notated that the Designee has signed on behalf of the person, e.g., if Ramesh Kumar is a designated signer for Suresh Kumar, then Ramesh Kumar would sign as, “Ramesh Kumar for Suresh Kumar,
Correction of Errors/Handling of Missed entries: